Quality Control
Committed to World-class Quality
Standardised Quality Testing Lab to Ensure Utmost Accuracy
Ensuring Precision,
Delivering Quality
Renuka Precision Plastics is committed to delivering Precision Plastics, and our rigorous quality testing and control processes ensure it. Our dedicated quality control team meticulously monitors every stage, guaranteeing that our products not only meet but exceed industry benchmarks. Trust Renuka Precision Plastics for unparalleled quality and consistency.
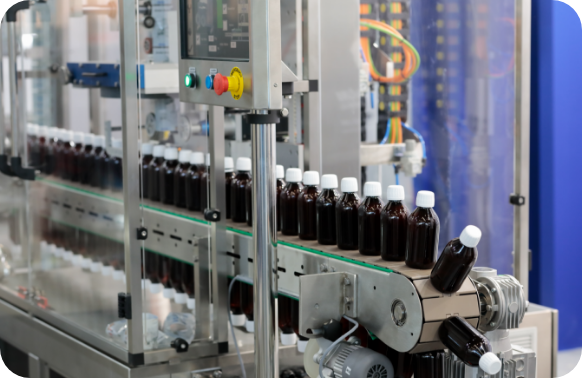
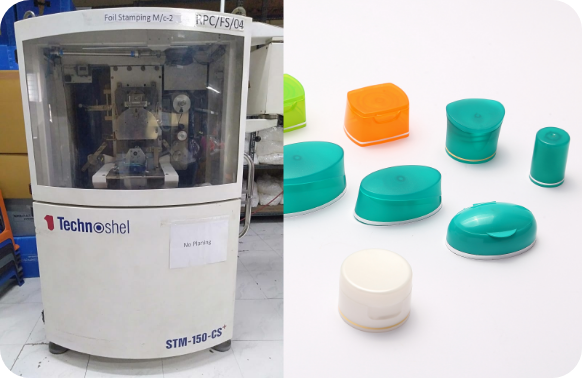
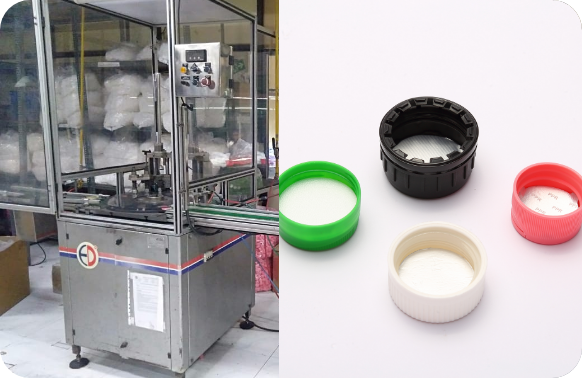
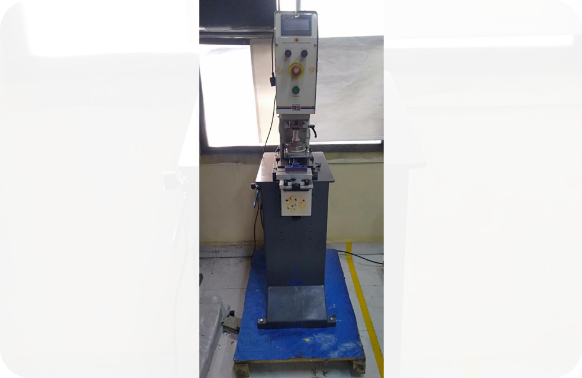
Secondary Operations
– Hot foil stamping
– Wad fixing
– Metalizing
– Pad printing
– Shrink sleeving
– Cap folding & slitting
– Wad fixing
– Metalizing
– Pad printing
– Shrink sleeving
– Cap folding & slitting
Automation
– Robotic injection moulding
– Electric process monitoring
– Automated quality control management
– Electric process monitoring
– Automated quality control management
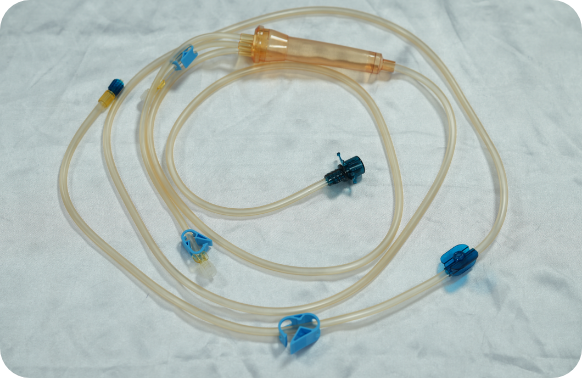
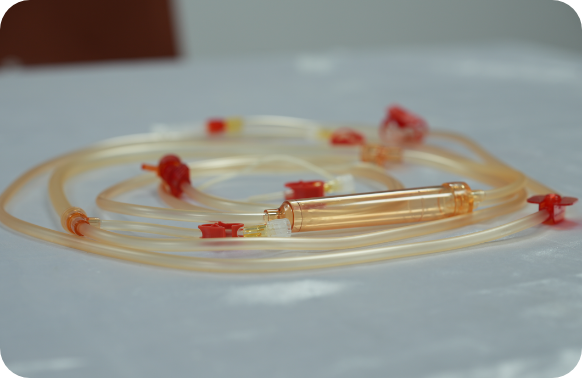
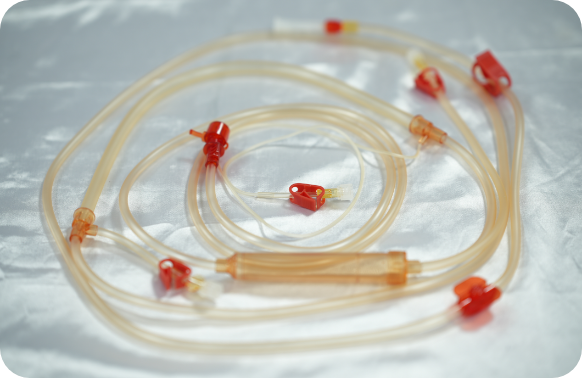
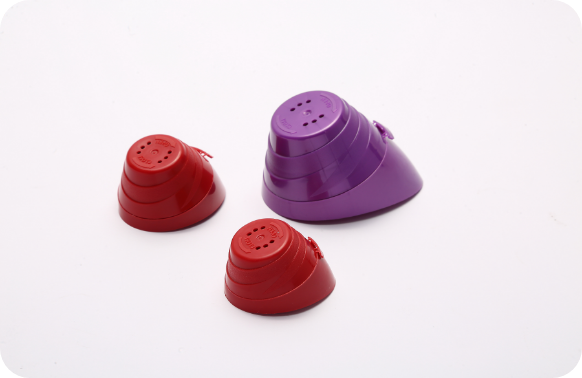
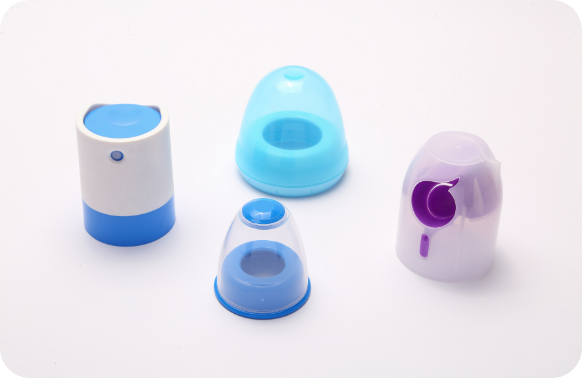
Component assembly
Once moulded, various plastic components are assembled together guided by the following system, which ensures precise alignment and consistency.
pick ➡place ➡ secure
This ensures precise alignment and consistency.
We Set The Standard
Five-star Quality
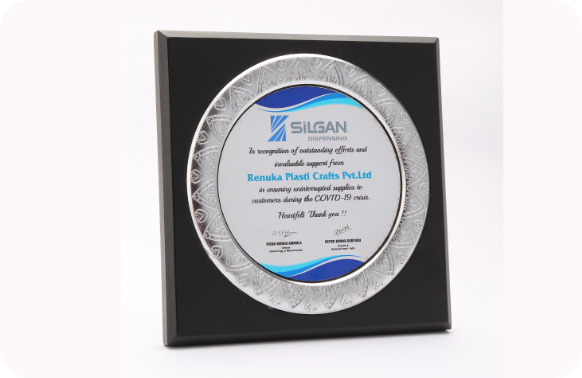
From design verification, material inspection and process control to visual inspection, we apply stringent quality control mechanisms that guarantee consistent and reliable results. This helps our products stand out flawlessly, increasing the shelf visibility & usability. We have authentic in-house mould & product quality validation facilities to ensure perfection.
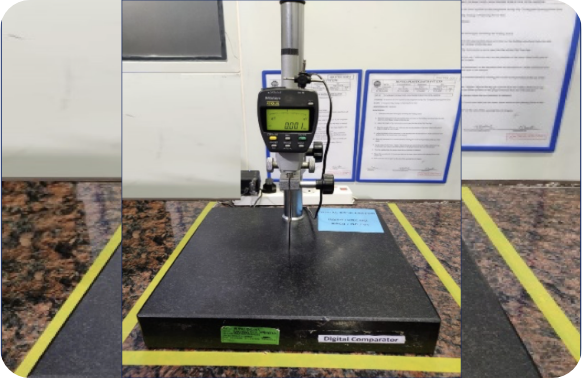
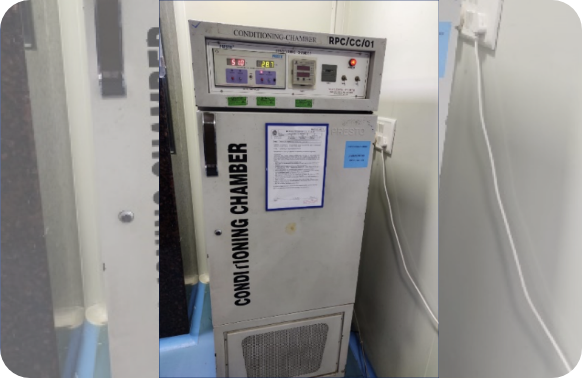
Quality Control Tests & Instruments
– Profile Projector
– Conditioning Chamber
– Torque Tester
– Universal Testing Machine
– Digital Comparator & Height Gauge
– Vacuum Leakage Tester
– Digital Vernier Callipers
– Digital Micrometre
– Bore Gauge
– Micrometer
– Surface Table
– Radius Gauge
– Thread Pitch Gauge
– VMS (Video Measurement System)
– Conditioning Chamber
– Torque Tester
– Universal Testing Machine
– Digital Comparator & Height Gauge
– Vacuum Leakage Tester
– Digital Vernier Callipers
– Digital Micrometre
– Bore Gauge
– Micrometer
– Surface Table
– Radius Gauge
– Thread Pitch Gauge
– VMS (Video Measurement System)
Quality Check Tests
– Melt Flow Index :
To study the polymer rheology & process parameter
– Colour Bleeding / Migration Test :
To study the colour migration from the master batch or pigments
– Dimensional Verification :
Ensures manufactured components are as per customer specification
– Universal Testing Machine Test :
To study the cap flip-open force, De-capping, Capping, & Compression tests by the Utm machine
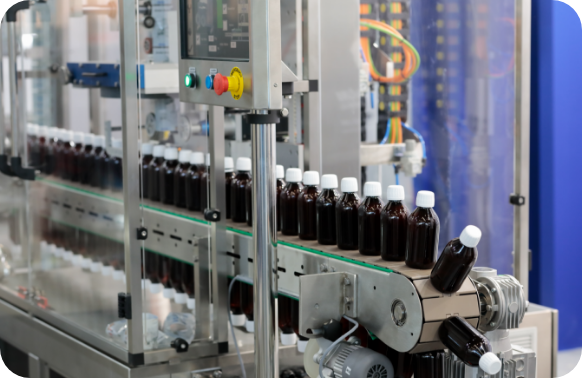
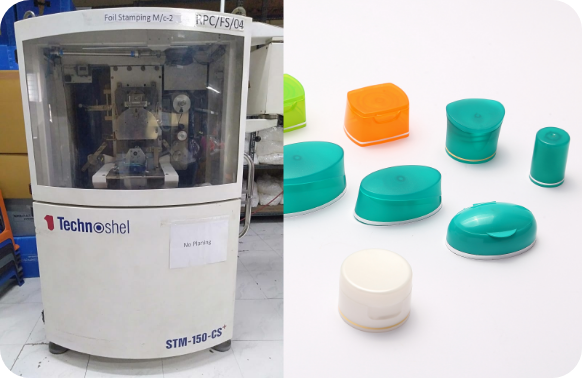
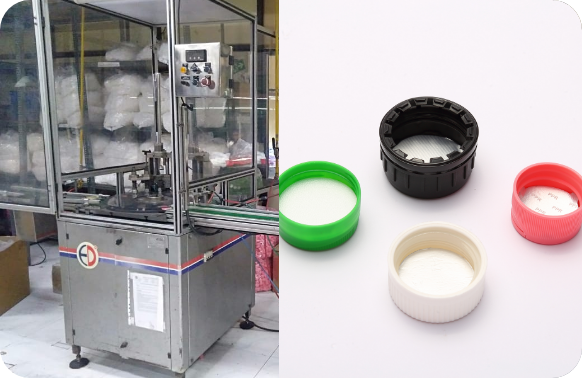
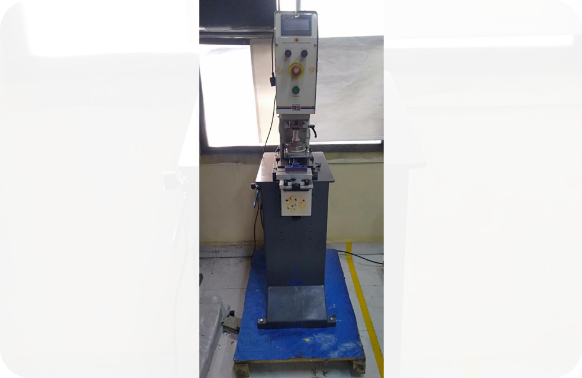
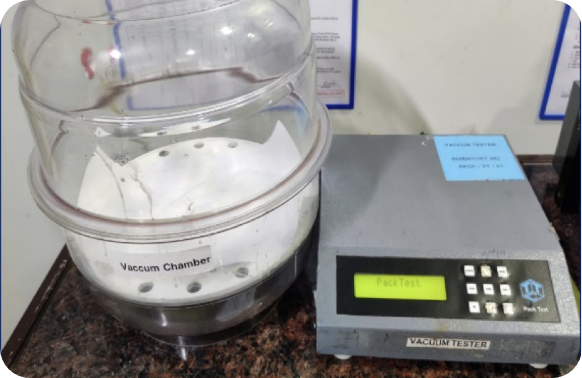
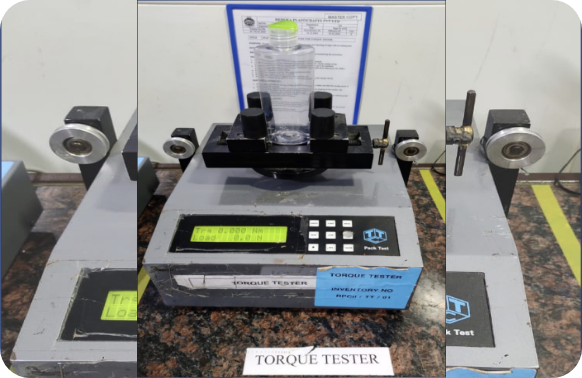
– Leakage Test :
To study any leakages after cap tment by air or water leakage
– Torque Test : To study the cap closing and cap Opening torque to ensure proper tment of caps
– Secure Seal Test : To ensure a cap or secure seal on mating team parts with the deaned condition
– Gas Volve Test : To ensure the components produced should withstand the required gas value at a certain test condition for a deaned time and also meet customer requirements
– Drop Test : To find out resistant to failure of caps when draft from a standard define height
– Torque Test : To study the cap closing and cap Opening torque to ensure proper tment of caps
– Secure Seal Test : To ensure a cap or secure seal on mating team parts with the deaned condition
– Gas Volve Test : To ensure the components produced should withstand the required gas value at a certain test condition for a deaned time and also meet customer requirements
– Drop Test : To find out resistant to failure of caps when draft from a standard define height